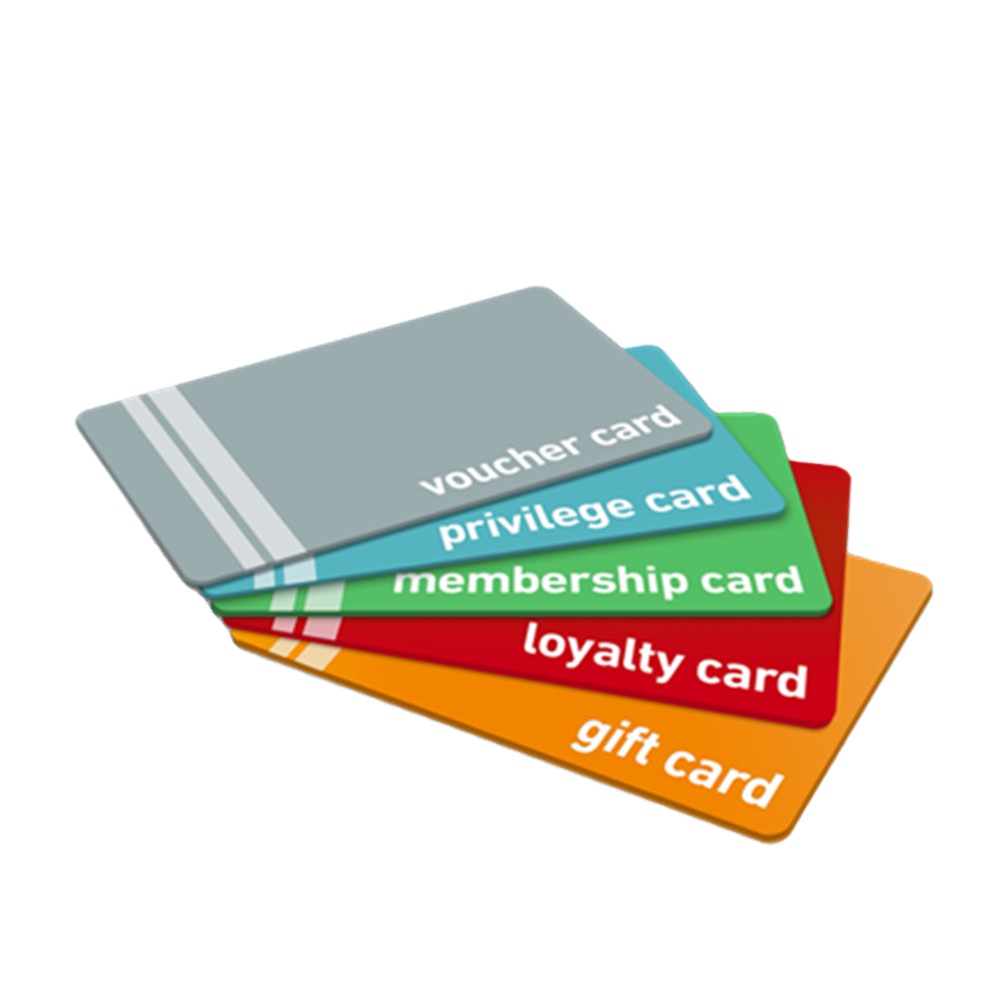
Who Benefits Most from MIFARE 1K Cards?
MIFARE 1K cards are durable, eco-friendly smart cards offering long-term use, reduced waste, and cost savings across various sectors and applications.
If you’ve ever used a contactless access card, tapped a transit pass, or swiped a loyalty card, you’ve interacted with a technology silently powering modern life: RFID Card Prelam Inlays. These unassuming components are the hidden heroes behind the durability and reliability of smart cards. But what makes them so resilient? Let’s dive into the engineering marvels that turn fragile electronics into everyday workhorses.
At its core, an RFID Prelam Inlay is a sophisticated “sandwich” of three critical layers:
The Microchip
Acting as the brain, this tiny semiconductor stores data—whether it’s your office ID number or payment credentials. Modern chips like NXP’s MIFARE or Impinj’s Monza series are designed to withstand millions of read/write cycles without degradation.
The Antenna
Crafted from materials like etched aluminum or ultrasonic-wound copper, the antenna is the card’s communicator. Its design isn’t random; precise engineering ensures optimal signal strength while resisting wear from bending or twisting.
The Substrate
High-performance PVC, PET, or polycarbonate forms the foundation. These materials are chosen for their mechanical strength, temperature resistance (-20°C to 70°C), and ability to shield internal components from moisture and physical stress.
What sets premium RFID Prelam Inlays apart is how these layers are fused. Manufacturers like ours use high-pressure lamination to eliminate air gaps, preventing delamination—a common failure point in cheaper cards.
Most card failures occur not because of the plastic exterior but due to flaws in the embedded electronics. Here’s how RFID Card Prelam Inlays tackle common durability challenges:
Ever sat on a wallet full of cards? Traditional magnetic stripe cards warp easily, but RFID Card Prelam Inlays are built differently. For example:
Independent testing shows that premium Prelam Inlays survive over 100,000 bending cycles—equivalent to a decade of daily use.
From icy parking garages to sweaty gym pockets, RFID cards face extreme conditions. RFID Card Prelam Inlays combat this with:
A hospital in Singapore, for instance, switched to PET-based Prelam Inlays for staff ID badges after cheaper cards failed in sterile washdown environments.
Durability isn’t just about surviving drops—it’s about consistent functionality. Advanced manufacturing techniques ensure:
Not all RFID Card Prelam Inlays are created equal. Here’s what separates industrial-grade products from budget options:
In our factory, automated optical inspection (AOI) systems scan every inlay sheet for microfractures or misaligned antennas. Combined with post-lamination X-ray checks, this ensures defects never reach customers.
Need a card that survives freezer temperatures? Or a transparent inlay for luxury hotel keycards? Custom designs are possible because:
To maximize card lifespan, ask suppliers:
✅ Compliance: Do inlays meet ISO 14443/15693 and IP68 standards?
✅ Antenna Process: Etched or wire-wound? The former excels in harsh environments.
✅ Lamination Guarantee: Look for warranties against delamination (e.g., 10-year warranties from top manufacturers).
✅ Custom Testing: Can they simulate your specific use case (e.g., salt spray testing for marine applications)?
Emerging trends are pushing durability further:
RFID Card Prelam Inlays are where cutting-edge materials science meets real-world reliability. By understanding their construction and manufacturing nuances, businesses can deploy cards that last longer, perform better, and reduce replacement costs. As a manufacturer pushing these boundaries, we’re committed to turning what seems like simple plastic into unsung heroes of the connected world.
Looking for a partner to engineer indestructible smart cards? Explore our customizable RFID Prelam Inlay solutions—where durability isn’t an afterthought, but the foundation.
[CTA: Contact our team to request free durability testing samples or custom antenna designs.]
Newest trends and common knowledge in RFID laundry tags.
MIFARE 1K cards are durable, eco-friendly smart cards offering long-term use, reduced waste, and cost savings across various sectors and applications.
Boost textile efficiency with RFID Inlays—track fabrics from cotton to shelf, cut costs, prevent errors, and unlock smart warehouse management.
Learn how to choose the right medical wristbands by focusing on technical adaptation, patient needs, and product quality to ensure medical safety.
As one of the top RFID Tag manufacturers in China, we specialize in high-quality RFID Tag and other RFID products designed to meet the diverse needs of various industries.
@ 2024 RFID Laundry Tag. All right reserved.
Didn’t find what you want? Ask our manager for help!